The Hugh Murray name has been a Dandenong fixture for more than 100 years.
The Buln Buln-based blacksmith turned his hand to driven tine and stump jump harrows in about 1900.
“Word got around his harrows were excellent. He then looked for somewhere to increase his production and get greater transport links,” Murray Agricultural Equipment operations manager Adrian Norton-Jones explained.
In 1915 he moved to Pickett Street in Dandenong – then the Gateway to Gippsland and closer to raw materials and transport links – where the business remains.
The Taylor family bought into the business in 1930 and fourth generation Jonathan Taylor manages sales and business development today.
“I feel very fortunate. I’m really excited for the future,” he said.
“We’re doing some great things here, and I think we’re going to continue to do great things.”
Mr Norton-Jones started with the company in a post-high school gap year in 1995.
“Dad just found a job ad in the Dandy Journal,” he said.
“He worked in Dandenong and it was easy to get to for him to drop me off here.”
His experience puts him in position to understand manufacturing challenges and lend a hand during busy periods.
“I know how everything’s made. I’ve made everything myself,” he said.
Mr Norton-Jones said the agriculture industry was vulnerable to the ups and downs of the weather and the economy.
“In the early ’80s, I think there were only two shifts before the recession with 25 employees,” he said.
“It went down to three or four days a week and only a couple of employees.
“We’ve been very financially conservative through history.
“We’ve always been able to keep things going either by trimming the workforce, which is unfortunate, or going to a reduced working week and trying to be more efficient.”
He said that hands rather than robots were behind almost the entire manufacturing process.
“It’d be nice to be able to make it a bit more efficient in the future, so we can reduce our costs and keep our prices where they are,” he said.
“It’s a matter of coming up with new ways to do it.”
Mr Norton-Jones said that “with Arrium OneSteel possibly closing down, we’d have to source overseas”.
The company used to buy some tines and bolts overseas but brought the purchases back to Australia.
“Even though it makes it more expensive, we use Australian-made where possible,” he said.
He said customers valued a product built in Australia rather than imported in pieces and assembled locally.
“The worm will turn. In America it’s all coming back – the high quality manufacturing is moving back to America from China,” he said.
“It will happen in Australia eventually as well.”
Murray was nominated for the Greater Dandenong Chamber of Commerce Business Awards last year.
“There’s enough agricultural manufacturers around but not many make harrows like we do now,” he said.
“Last year was one of our best years for our last five years.
“But it’s getting to the stage where we need to produce varied products.
“To the future, we’ve got a few products that we’re going to bring to market next year.
“We have plans to, hopefully, vertically integrate over the next five years.
“If we don’t do that, we’ll eventually cease, unfortunately.
“We were turning over $1.5 million in the mid-’90s.
“Now we’re at about $1 million.
“We’re doing about 2000 units a year now, which is probably 40 per cent of what it was 15 years ago, unfortunately.”
He said the Riverina of New South Wales was returning to harrowing.
“Which is good for us,” he said.
“They believe they get better yields.”
Murray produces about 15 products, taking care of the pasture for the dairy and grazing industries.
“That just knocks the manure and the hoof prints around so it keeps a nice grass cover and keeps the pasture in good condition,” Mr Norton-Jones said.
“The livestock won’t eat where they’ve defecated.
“The rest of our harrows are really for the broad acre seeding style – the west of NSW, the Wimmera Mallee of Victoria – those sort of areas where they’ve got the large properties.”
Harrows are the top crop
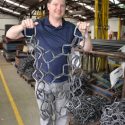
Digital Editions
-
Developer donates home for homeless
Purchase this photo from Pic Store: 497869 Dandenong South-based Alapont Development has donated a brand-new house in Pakenham to homelessness agency WAYSS for families in…