Nissan’s Dandenong casting plant is still producing parts 35 years after it opened its doors.
The automotive manufacturer celebrated the milestone on Thursday 16 November.
The plant sits on 90,000 square metres, employs 192 skilled workers and runs three shifts every day.
It annually produces about 2.6 million die-cast aluminium parts and more than 16,000 tow bars with an export value of $82.5 million.
Nissan Casting Australia managing director Peter Jones said the plant’s work was critical to the global business.
“We have exclusive supply contracts awarded by Nissan Global that will keep the plant operating well into the next decade,” he said.
“Nissan Casting Australia is defying the belief that automotive manufacturing doesn’t have a place in our country.
“If you want evidence of Made in Australia you’ll find it here.”
Nissan has worked with the CSIRO to develop precision technology and invested $11 million in new tooling and other equipment.
“Our quality department uses the same kind of measuring machines and granite tables used by Formula One teams,” Mr Jones said.
“These parts are so precise that they match up exactly with parts made in Japan to a tolerance of 15 microns, less than the diameter of a human hair.
“And it’s this precision and quality that has earned us exclusive contracts for the supply of specific parts.”
The plant creates 60 different parts specific to oil pans, gearbox and final-drive housing, and electric vehicles through high and low-pressure die casting, precision machining, component assembly and accessories manufacturing.
“In addition to this, our parts feature on over 30 different overseas models from a variety of our brands, including Nissan, Infiniti and Renault,” Mr Jones said.
“This includes the just-released New Nissan LEAF, which includes an EV water jacket Inverter, Inverter cover, Inverter case and Motor Stator Housing that all come directly out of Dandenong. This is significant for Australian manufacturing.”
Dandenong plant a solid performer for Nissan
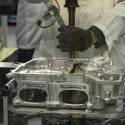
Digital Editions
-
Dandenong pair added to Vic Country lineup
A pair of Dandenong Stingrays are set to make their first appearances at the Under-18s Boys National Championships on Saturday at Ikon Park. Halfback Jasper…